Understanding the Pitfalls of Poor Warehouse Layouts
In the realm of logistics and supply chain management, the importance of an efficient warehouse layout cannot be overstated. A well-designed warehouse layout is essential for optimizing operations, improving productivity, and ultimately enhancing the overall performance of a business. Conversely, a poor warehouse layout can lead to a myriad of problems, impacting everything from order fulfillment to employee morale. In this article, we will delve into the characteristics and consequences of a subpar warehouse layout.
The Anatomy of a Poor Warehouse Layout
A poor warehouse layout is characterized by a variety of factors that hinder the smooth flow of operations. One of the primary elements contributing to an inefficient layout is inadequate space utilization. Warehouses often deal with limited square footage, and improper utilization of available space can result in congestion, reduced storage capacity, and inefficient material handling.
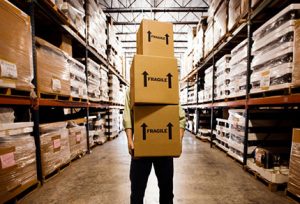
Moreover, a lack of proper zoning is another hallmark of a suboptimal layout. Without well-defined zones for receiving, storage, picking, and shipping, chaos can ensue. This lack of organization can lead to delays, errors, and increased operational costs. A good warehouse layout should be designed with a clear understanding of the workflow, ensuring a logical and streamlined process from the moment goods enter the facility to when they leave.
The Impact on Operational Efficiency
The consequences of a poor warehouse layout are far-reaching and can significantly impact operational efficiency. One of the most notable effects is an increase in order fulfillment times. Inefficient layouts often result in longer travel distances for workers and equipment, leading to delays in picking and packing orders. This not only affects customer satisfaction but also puts additional strain on the workforce.
Furthermore, a poorly designed layout can contribute to an increase in errors. When different products are haphazardly stored or when the picking paths are not optimized, the likelihood of mispicks and shipping errors rises. This not only results in additional costs for rectifying mistakes but also damages the reputation of the business.
Another critical aspect affected by a subpar warehouse layout is employee morale and safety. Inadequate space and poorly planned traffic flow can create hazardous working conditions. Accidents, injuries, and fatigue are more likely in an environment where employees are navigating through cluttered aisles or struggling to access stored goods. This not only impacts the well-being of the workforce but also contributes to increased absenteeism and turnover rates.
The Financial Toll of Inefficiency
Beyond the operational challenges, a poor warehouse layout can take a significant financial toll on a business. Inefficient space utilization often leads to the need for larger facilities or additional storage space, driving up real estate costs. The increased labor hours required to navigate through a poorly designed layout contribute to higher labor costs, further impacting the bottom line.
Moreover, the impact on inventory management should not be underestimated. Inadequate storage practices can result in stockouts or excess inventory, both of which have financial implications. Stockouts can lead to lost sales and dissatisfied customers, while excess inventory ties up capital and incurs holding costs.
The Role of Technology in Warehouse Optimization
Fortunately, advancements in technology provide solutions for optimizing warehouse layouts. Warehouse management systems (WMS) and automated technologies can help streamline operations by providing real-time visibility into inventory, automating order picking processes, and optimizing storage space.
WMS software, in particular, can assist in creating efficient picking routes, managing inventory levels, and improving overall warehouse organization. Automated guided vehicles (AGVs) and robotics can enhance material handling processes, reducing the reliance on manual labor and minimizing the risk of accidents.
Designing a Blueprint for Success
To overcome the challenges associated with poor warehouse layouts, businesses must prioritize thoughtful design and continuous improvement. Investing in a well-designed layout from the outset can save both time and money in the long run. Key considerations include:
Space Utilization: Maximize storage space by implementing effective storage systems such as pallet racking and mezzanines. Ensure that aisles are wide enough to facilitate smooth traffic flow.
Zoning and Organization: Clearly define zones for different warehouse activities. This includes dedicated areas for receiving, storage, picking, packing, and shipping.
Technology Integration: Leverage warehouse management systems and automation technologies to enhance efficiency, accuracy, and overall operational performance.
Flexibility: Design the layout with scalability in mind. A flexible layout can adapt to changes in demand, inventory levels, and business growth.
Employee Input: Seek input from warehouse staff, as they are on the front lines of operations. Their insights can provide valuable perspectives on potential improvements and challenges.
Conclusion: A Blueprint for Efficiency
In conclusion, the impact of a poor warehouse layout extends far beyond the physical constraints of a facility. It affects operational efficiency, employee morale, and the financial health of a business. By investing time and resources in designing a well-organized and optimized layout, businesses can create a blueprint for success in the competitive landscape of logistics and supply chain management. The integration of technology and a commitment to continuous improvement are key elements in achieving a warehouse layout that not only meets current needs but also sets the stage for future growth and success.