Optimizing Loading Dock Spacing for Efficient Operations
Loading docks play a crucial role in the logistics and supply chain industry, serving as the focal point for the seamless movement of goods in and out of warehouses. One often overlooked aspect in the design and layout of these loading docks is the distance between them. The question arises: How far apart should loading docks be for optimal efficiency? In this article, we will explore the key considerations and factors that influence the spacing of loading docks.
The Importance of Loading Dock Spacing
Loading dock spacing is a critical element in the overall efficiency of a warehouse or distribution center. The right spacing ensures smooth operations, minimizes congestion, and maximizes the throughput of goods. Conversely, inadequate spacing can lead to bottlenecks, delays, and increased operational costs.
1. Dock Door Configurations
One of the primary factors influencing loading dock spacing is the configuration of dock doors. Different warehouses have varying door configurations, such as straight-line docks, angled docks, or wrap-around docks. The type of configuration will impact the layout and spacing required between individual docks.
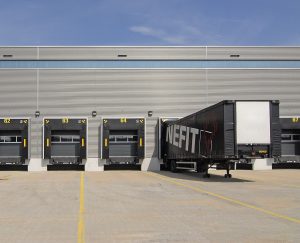
Straight-line docks, where the doors are aligned in a linear fashion, may allow for a more compact layout. On the other hand, angled or wrap-around docks might necessitate more space between docks to accommodate the turning radius of trucks and provide maneuvering space.
2. Vehicle Size and Turning Radius
The size of the vehicles accessing the loading docks is another critical consideration. Larger trucks with extended trailers may require more space for maneuvering and turning. Understanding the turning radius of these vehicles is essential in determining the optimal distance between loading docks.
Warehouses that frequently deal with a variety of vehicle sizes should consider a more generous spacing between docks to accommodate different types of trucks without causing congestion or accessibility issues.
3. Material Handling Equipment
In addition to accommodating trucks, loading dock spacing should also consider the movement of material handling equipment. Forklifts, pallet jacks, and other machinery play a pivotal role in the efficient transfer of goods within the warehouse. Sufficient space between loading docks is necessary to facilitate the smooth movement of this equipment.
Careful planning is required to ensure that the spacing allows for the safe and efficient operation of material handling equipment without compromising the overall flow of goods.
Calculating Optimal Loading Dock Spacing
Determining the ideal distance between loading docks involves a combination of industry best practices, regulations, and the specific needs of the warehouse. While there is no one-size-fits-all solution, certain calculations and guidelines can aid in optimizing loading dock spacing.
1. Industry Standards
Several industry organizations provide guidelines for loading dock design and layout. These standards often include recommendations for dock spacing based on the type of operation, the volume of goods handled, and the size of the facility. Warehouse managers and designers should refer to these standards to ensure compliance and optimal performance.
2. Turning Templates and Software
The use of turning templates and simulation software can be invaluable in determining the optimal loading dock spacing. These tools allow designers to visualize the movement of trucks and material handling equipment within the warehouse space. By inputting specific dimensions and characteristics, designers can assess different scenarios to arrive at the most efficient layout.
3. Future Expansion Plans
Forward-thinking warehouse design considers future expansion plans. Loading dock spacing should not only meet current requirements but also allow for scalability. As businesses grow, the ability to easily add more loading docks without significant disruption becomes a valuable asset. Planning for future expansion minimizes the need for costly retrofits or reconfigurations.
Challenges and Solutions
While optimizing loading dock spacing is essential, warehouses may face challenges in achieving the ideal layout. Common challenges include limited available space, budget constraints, and zoning regulations. However, innovative solutions can address these challenges and still result in an efficient loading dock layout.
1. Vertical Expansion
In situations where horizontal space is limited, warehouses can explore vertical expansion options. Multi-level loading docks, though more complex to design and implement, can maximize the use of available space. Vertical expansion allows for a higher density of loading docks without sacrificing efficiency.
2. Flexible Design Features
Flexibility in design is key to overcoming challenges associated with loading dock spacing. Incorporating features such as adjustable dock positions, modular loading dock systems, and flexible traffic patterns enables warehouses to adapt to changing operational needs. This adaptability ensures that the loading dock layout remains efficient over time.
3. Collaboration with Stakeholders
Engaging with key stakeholders, including transportation providers, suppliers, and regulatory authorities, can provide valuable insights into the specific requirements of the operation. Collaborative efforts can lead to a loading dock layout that not only meets industry standards but also addresses the unique challenges and opportunities of the particular supply chain.
Conclusion
In conclusion, the optimal spacing between loading docks is a critical factor in the efficiency and productivity of warehouse operations. Considerations such as dock door configurations, vehicle size, turning radius, material handling equipment, and adherence to industry standards all play a role in determining the ideal layout.
Warehouse managers and designers must employ a strategic approach, utilizing industry guidelines, simulation tools, and collaborative efforts to design loading dock layouts that not only meet current needs but also allow for future expansion. Overcoming challenges with innovative solutions ensures that loading docks become a seamless and efficient hub for the movement of goods within the supply chain.