What Are the 2 Types of Cold Chain?
The cold chain is a crucial logistical process designed to maintain the quality and safety of temperature-sensitive products throughout the supply chain. This is especially important for industries like pharmaceuticals, food, and biotechnology, where maintaining specific temperatures is essential. Understanding the two primary types of cold chains—active and passive—is key to ensuring the effectiveness of cold storage and transportation. This article explores these two types in detail, highlighting their characteristics, benefits, and applications. Why Certain Items Don’t Belong in Cold Storage
Understanding the Cold Chain
The cold chain refers to a temperature-controlled supply chain that maintains a consistent temperature from the point of origin to the final destination. This is critical for preserving the quality and safety of products sensitive to temperature fluctuations. The cold chain encompasses various stages, including production, storage, transportation, and distribution, and relies on specialized equipment and practices to ensure temperature consistency.
The Two Types of Cold Chain
1. Active Cold Chain
The active cold chain involves the use of mechanical cooling systems to maintain a specific temperature throughout the entire supply chain. This type of cold chain relies on refrigeration units and other temperature-control technologies to actively manage and monitor the temperature of goods during storage and transportation.
Characteristics of Active Cold Chain
Temperature Control: Active cold chains use refrigeration systems to maintain a precise temperature range. This includes refrigerated trucks, climate-controlled warehouses, and refrigerated shipping containers.
Continuous Monitoring: Temperature sensors and monitoring systems are used to continuously track and record temperature data. This ensures that any deviations from the desired temperature are detected and addressed promptly.
Energy-Dependent: Active cold chains rely on a constant power supply to operate refrigeration units and other cooling equipment. This makes them energy-intensive but effective in maintaining consistent temperatures.
Benefits of Active Cold Chain
Precise Temperature Control: Active cold chains provide accurate and reliable temperature management, reducing the risk of spoilage or degradation of temperature-sensitive products.
Flexibility: They can accommodate a wide range of temperature requirements, making them suitable for various types of goods, including pharmaceuticals, perishable foods, and biological samples.
Real-Time Monitoring: Continuous monitoring allows for immediate response to temperature deviations, ensuring the integrity of the products throughout the supply chain.
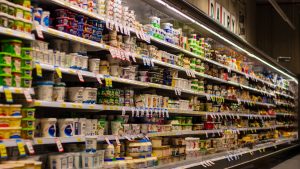
Applications of Active Cold Chain
Pharmaceuticals: Active cold chains are essential for transporting vaccines, medications, and other temperature-sensitive drugs that require strict temperature control.
Food Industry: Perishable foods such as meat, dairy, and frozen items rely on active cold chains to maintain freshness and safety.
Biotechnology: Biological samples and research materials often require active cold chains to preserve their viability and integrity.
2. Passive Cold Chain
The passive cold chain relies on insulating materials and temperature-stabilizing techniques to maintain temperature without the use of active refrigeration systems. This type of cold chain uses materials like insulated boxes, gel packs, and dry ice to keep products at the required temperature during transit.
Characteristics of Passive Cold Chain
Temperature Stability: Passive cold chains rely on the thermal properties of insulating materials and cooling agents to maintain temperature. This includes insulated containers and cool packs that provide temperature control without active refrigeration.
Limited Monitoring: Temperature monitoring in passive cold chains is typically less sophisticated compared to active systems. Monitoring devices may be used but are often less integrated into the supply chain.
Energy Independence: Passive cold chains do not require an external power source for cooling, making them more suitable for short-term storage and transportation.
Benefits of Passive Cold Chain
Cost-Effective: Passive cold chains generally require less energy and infrastructure investment compared to active systems, making them a more cost-effective solution for certain applications.
Flexibility: They are ideal for situations where access to power is limited or where refrigeration infrastructure is not feasible.
Simplicity: Passive systems are often simpler to implement and manage, making them suitable for small-scale or one-time shipments. https://commgen.com.au/product/cold-storage-design-construction/
Applications of Passive Cold Chain
Emergency Shipments: Passive cold chains are useful for transporting temperature-sensitive items in emergency situations where active cooling may not be available.
Short-Term Storage: Items that require only brief periods of temperature control can benefit from passive cold chains, such as in smaller shipments or during local distribution.
Temperature-Stable Goods: Products with a longer allowable temperature range can often be transported using passive cold chain methods.
Choosing Between Active and Passive Cold Chains
Selecting between an active and passive cold chain depends on various factors, including the nature of the product, the duration of transport, and the required temperature range.
Considerations for Active Cold Chain
High Value and Sensitivity: Products that are highly sensitive to temperature fluctuations, such as pharmaceuticals and high-value perishables, benefit from the precise control offered by active cold chains.
Long-Distance Transport: Active systems are more suitable for long-distance or international shipments where maintaining a consistent temperature is crucial.
Considerations for Passive Cold Chain
Cost and Infrastructure: For situations where budget constraints or limited infrastructure make active cold chains impractical, passive systems provide a viable alternative.
Short-Term Needs: Passive cold chains are ideal for short-term storage or local deliveries where the temperature control requirements are less stringent.
Conclusion
Understanding the two types of cold chains—active and passive—is essential for managing temperature-sensitive products effectively. Active cold chains offer precise temperature control and continuous monitoring, making them ideal for high-value and sensitive items. Passive cold chains, on the other hand, provide a cost-effective and simpler solution for short-term temperature control and less sensitive products. By selecting the appropriate cold chain method based on the specific needs of your products, you can ensure their quality and safety throughout the supply chain. Why Certain Items Don’t Belong in Cold Storage