Managing Cold Storage Demands: Strategies for Efficiency and Cost Control
Cold storage plays a crucial role in preserving perishable products across industries, from food and beverages to pharmaceuticals. As consumer demand rises and supply chains grow more complex, managing cold storage demands has become increasingly challenging. This article provides insights into strategies for meeting cold storage demands effectively, ensuring both quality and operational efficiency.
Understanding Cold Storage Demand Fluctuations
Cold storage demands vary widely throughout the year, influenced by seasonal peaks, market trends, and changing consumer behaviors. Efficient management requires a clear understanding of these fluctuations to ensure sufficient capacity and avoid overloading or underutilization.
The Impact of Seasonal Variations
Cold storage facilities experience significant seasonal variations, especially in industries like agriculture and food. Harvest seasons bring an influx of fresh produce needing immediate storage, while holidays and events often increase demand for food storage.
Harvest Seasons: During peak harvest times, facilities must manage large volumes of produce, often requiring additional storage or faster turnover.
Holiday Seasons: The demand for holiday-specific products, like frozen meals or specialty ingredients, can surge and require temporary adjustments to storage capacity.
Changes in Consumer Demand
Consumer trends, such as the rise in online grocery shopping and demand for fresh, organic foods, affect cold storage needs. Cold storage facilities must adapt to these shifts by balancing demand forecasting with real-time flexibility.
E-commerce Growth: With more consumers ordering groceries online, demand for cold storage of fresh produce and prepared foods has grown.
Health-Conscious Consumers: Increased interest in fresh, organic, and minimally processed foods requires more sophisticated storage solutions to maintain quality.
Optimizing Cold Storage Space and Inventory
Efficient space utilization and inventory management are essential for handling cold storage demands. By maximizing storage capacity and streamlining inventory turnover, facilities can reduce waste and improve response times to changes in demand.
Implementing a First-In, First-Out (FIFO) System
A FIFO system ensures that older products are used or shipped first, reducing spoilage and keeping inventory fresh. This system is particularly valuable in cold storage where perishability is a major concern.
Efficient Rotation: FIFO prevents older products from being stored too long, maintaining freshness and minimizing waste.
Improved Organization: Labeling and organizing products by entry date streamlines the picking process, making it easier for staff to locate items.
Maximizing Storage Density
To maximize storage space, many facilities adopt high-density storage solutions, such as mobile shelving or racking systems, which allow more products to be stored within the same footprint.
Compact Storage Solutions: Implementing vertical racks or compact shelving units increases storage density without compromising accessibility.
Cold Zone Segmentation: Dividing storage areas based on product temperature needs can further optimize space and improve temperature control efficiency.
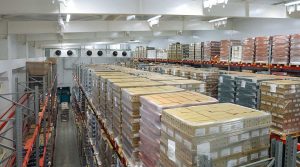
Utilizing Technology for Demand Forecasting and Monitoring
Modern cold storage facilities rely on technology to forecast demand, monitor inventory, and optimize operational efficiency. These technologies offer real-time data, enabling facilities to adapt to fluctuations in demand and make proactive adjustments. Find us here.
Demand Forecasting Software
Forecasting software analyzes historical data, industry trends, and seasonal factors to predict future cold storage needs. By understanding potential fluctuations in demand, facilities can prepare accordingly.
Accurate Inventory Planning: Demand forecasting allows for precise inventory management, reducing excess storage and minimizing stockouts.
Resource Allocation: Forecasting enables facilities to allocate resources effectively, ensuring sufficient staffing and equipment during peak times.
Real-Time Monitoring Systems
Real-time monitoring systems track inventory levels, product conditions, and equipment performance, offering a comprehensive view of facility operations.
Temperature and Humidity Sensors: Continuous monitoring of storage conditions ensures products are kept within ideal ranges, reducing spoilage risk.
Inventory Tracking: Automated inventory tracking reduces human error, increases accuracy, and enables quick response to changing demand levels.
Maintaining Efficiency in Energy Use
Energy is one of the largest costs in cold storage. Effective energy management helps facilities manage high demand without excessive costs or compromising temperature control.
Energy-Efficient Cooling Systems
Upgrading to energy-efficient cooling systems reduces energy consumption and ensures reliable temperature control. Many modern systems include variable-speed compressors and advanced sensors that adapt cooling based on demand.
Reduced Operating Costs: Energy-efficient systems decrease electricity costs while maintaining cold temperatures.
Improved Temperature Stability: Advanced cooling systems stabilize temperatures, reducing fluctuations that could impact product quality.
Insulation and Door Management
Proper insulation and managing door openings help maintain temperatures, reducing energy demands and preventing the ingress of warm air.
Enhanced Insulation: Insulating walls, floors, and ceilings minimizes heat transfer and reduces cooling load.
Efficient Door Usage: Minimizing door openings and installing air curtains or strip curtains can prevent temperature loss, preserving the cold environment.
Enhancing Cold Storage Flexibility
Flexibility is key to managing cold storage demands, especially when dealing with short-term fluctuations or emergencies. Having flexible storage options allows facilities to adapt to varying product volumes and temperatures.
Modular Cold Storage Units
Modular cold storage units can be added or removed as demand changes. These units provide a scalable solution, allowing facilities to increase capacity temporarily or for specific products.
Temporary Capacity Boost: Modular units offer extra space during peak seasons or for short-term storage needs.
Product Segmentation: Facilities can separate different product types by using modular units for specific temperature requirements.
Outsourcing Additional Cold Storage
When internal capacity is limited, outsourcing to third-party cold storage providers can help meet unexpected demand. This solution is ideal for managing overflow during peak times without needing permanent facility expansion.
Cost-Effective Overflow Management: Using external facilities during peak times prevents the costs of expanding permanent storage.
Reduced Operational Pressure: Outsourcing allows facilities to focus on core operations while meeting seasonal demand fluctuations.
Ensuring Compliance and Quality Standards
Maintaining high standards for quality and compliance is essential in cold storage. Regulatory compliance ensures that products are stored safely and that the facility meets industry standards, particularly in industries like food and pharmaceuticals.
Adhering to Regulatory Guidelines
Cold storage facilities must adhere to regulations specific to their industry, which outline temperature control, sanitation, and safety requirements. Staying updated on regulatory changes helps facilities remain compliant and avoid fines or product recalls.
Industry-Specific Requirements: Regulatory bodies, such as the FDA for food and health organizations for pharmaceuticals, mandate strict guidelines for cold storage.
Regular Audits and Inspections: Conducting routine audits ensures that storage conditions, equipment, and processes comply with industry standards.
Training Staff on Cold Storage Protocols
Properly trained staff are essential for managing cold storage demands effectively. Employees should understand cold storage protocols, including temperature monitoring, inventory management, and safety practices.
Temperature Monitoring Procedures: Staff should know how to use monitoring equipment and respond to temperature fluctuations.
Safety and Handling: Training in safe handling and storage practices reduces the risk of contamination and spoilage.
Conclusion: Strategies for Meeting Cold Storage Demands Effectively
Managing cold storage demands requires a blend of effective forecasting, optimized storage solutions, energy efficiency, and flexibility. By understanding demand fluctuations and adopting modern technologies for forecasting and monitoring, facilities can optimize inventory management and improve response times. Furthermore, energy-efficient practices and flexible storage solutions help keep costs down while maintaining product quality. https://commgen.com.au/product/tretight-inflatable-dock-seals/