Choosing the Right Size for Industrial Cold Storage Rooms
Industrial cold storage rooms are essential for businesses that need to store large quantities of perishable or temperature-sensitive goods. Selecting the right size for these rooms is crucial to ensure efficiency, reduce costs, and maintain the quality of stored products. This article explores the factors to consider when choosing the size for industrial cold storage rooms and provides practical advice for making an informed decision.
1. Understanding Your Storage Needs
Before determining the size of your cold storage room, it’s important to thoroughly understand your specific storage needs. This involves evaluating the types of products you will store, their volume, and their unique requirements.
1.1 Types of Products
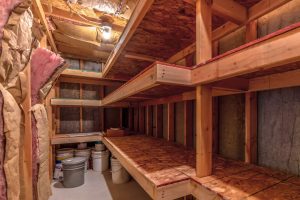
Different products have different storage requirements, which can influence the size of the cold storage room:
- Perishables: Fresh produce, dairy products, and meat require consistent refrigeration and proper ventilation. The size should accommodate the volume of these items and allow for adequate airflow.
- Frozen Goods: Frozen foods need very low temperatures. Ensure that the room is large enough to support the required refrigeration capacity and maintain consistent temperatures throughout.
- Pharmaceuticals: Temperature-sensitive pharmaceuticals require precise temperature control and monitoring. The room must be sized to fit specialized equipment for compliance and efficacy.
1.2 Inventory Volume
Estimating the volume of inventory is a crucial step in determining the appropriate size for your cold storage room:
- Current Inventory: Measure the total volume of products, including packaging. This helps in determining the minimum space needed.
- Future Growth: Consider future increases in inventory to avoid frequent resizing or expansion of the storage room.
- Turnover Rate: Higher turnover rates may require additional space to facilitate easier access and reduce congestion.
2. Calculating Cold Storage Room Size
Once you have a clear understanding of your storage needs, you can calculate the appropriate size for your cold storage room. This involves assessing several key factors.
2.1 Space Requirements
Calculate the total space required based on the volume of goods and the type of storage systems you plan to use:
- Product Dimensions: Measure the dimensions of the products and their packaging to estimate the space needed.
- Storage Systems: Consider the type of shelving, racking, or pallet systems you will use. These systems affect how efficiently you use available space.
2.2 Temperature Control Considerations
Effective temperature control is essential for maintaining product quality. The size of the cold storage room should support the necessary refrigeration and insulation systems:
- Refrigeration Capacity: Choose a refrigeration system that can handle the thermal load of the room. The size of the room affects the efficiency of the cooling system.
- Insulation: Ensure that the room is well-insulated to maintain temperature and reduce energy consumption. Proper insulation also impacts the overall size of the room.
2.3 Layout and Access
The layout and accessibility of the cold storage room impact its functionality and efficiency:
- Aisle Widths: Design aisles wide enough for easy movement of personnel and equipment. This helps in minimizing damage and improving operational efficiency.
- Loading and Unloading: Ensure there is adequate space for loading and unloading activities. This includes designing entry and exit points for delivery trucks and handling equipment.
3. Optimizing Cold Storage Room Design
Optimizing the design of your cold storage room can enhance efficiency and reduce operational costs. Consider the following strategies to ensure you get the most out of your space.
3.1 Maximizing Storage Density
Increasing storage density can help you make the most of your available space:
- Vertical Storage: Use high shelving or racking systems to utilize vertical space. This can significantly increase your storage capacity without expanding the room’s footprint.
- Modular Racking: Implement modular racking systems that can be adjusted based on changing storage needs.
3.2 Incorporating Technology
Technology can improve the efficiency and management of your cold storage room:
- Temperature Monitoring: Install temperature sensors and monitoring systems to maintain optimal conditions and receive alerts for any deviations.
- Automated Systems: Consider automated storage and retrieval systems to streamline operations and reduce manual handling.
3.3 Energy Efficiency
Reducing energy consumption is both cost-effective and environmentally friendly:
- Energy-Efficient Equipment: Use energy-efficient refrigeration systems and lighting to reduce operational costs.
- Insulation and Sealing: Ensure that the room is properly insulated and sealed to minimize energy loss and maintain consistent temperatures.
4. Compliance and Safety
Compliance with industry regulations and safety standards is essential for cold storage rooms:
4.1 Regulatory Requirements
Ensure that your cold storage room meets all regulatory requirements for temperature control, hygiene, and safety:
- Industry Standards: Adhere to industry-specific standards and guidelines for cold storage, such as those for food safety or pharmaceutical storage.
- Documentation: Maintain accurate records of temperature monitoring, maintenance activities, and compliance with regulations.
4.2 Safety Measures
Implement safety measures to protect personnel and products:
- Emergency Procedures: Establish emergency procedures and ensure that they are communicated to all personnel.
- Training: Provide training for staff on safe handling practices and emergency response.
Conclusion
Choosing the right size for industrial cold storage rooms involves understanding your storage needs, calculating space requirements, and optimizing the design for efficiency and compliance. By carefully considering factors such as product types, inventory volume, temperature control, and layout, you can create a cold storage environment that meets your operational requirements and enhances overall performance. Investing time and resources into planning and design will pay off in improved efficiency, reduced costs, and better product preservation.